CPECC参建俄罗斯AGPP项目第一列生产线投产纪实
记者6月17日获悉,工程建设有限公司(CPECC)参与建设的阿穆尔天然气处理厂(AGPP)项目第一列生产线投产庆典仪式近期在俄罗斯自由城项目现场举行,并收到贺信。这是中俄能源合作结出的又一丰硕成果。
AGPP项目是俄罗斯远东地区最大的基础设施项目之一,也是中俄东线的源头工程,设计年加工天然气420亿立方米,生产商品氦1万吨。项目位于俄罗斯阿穆尔州自由城,建设周期8年,分5期建设,共有6条生产线,满负荷生产后,将成为世界上最大的天然气加工企业之一,对俄罗斯国民经济、东西伯利亚和远东地区的发展都具有重要意义。此次投产的第一列生产线,年处理量为70亿立方米。
2017年4月,工程建设有限公司(CPECC)与俄罗斯NIPIGAS公司签署AGPP项目P2标段(非专利单元)EPC合同,这也是CPECC进入俄罗斯市场的第一个项目。项目设计由英国福陆公司承担,施工由土耳其YAMATA公司承担。不同于以往的项目组织模式,极寒施工环境、新冠肺炎疫情蔓延等影响,给项目执行带来巨大挑战。
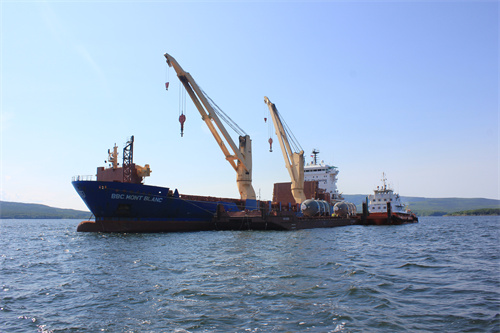
超大件设备从海运重吊船换装至内河驳船。
舞动设计龙头
设计是项目建设的龙头专业。CPECC发挥自有设计力量优势,由项目设计部负责设计管理与协调,西南分公司加入项目设计,与福陆公司联合完成一期工程设计,复制和优化二至五期工程设计。
设计工作在中、英、俄3种工作语言和国内外5个办公点展开。面对国际知名公司,中方设计人员既能向合作伙伴虚心学习欧美工程设计体系和厂商文件审查、内部文件传递及互审等精细化管理方法,又敢于坚持自己的意见。
今年2月,AGPP项目核心装置——首台压缩机组启动马达进行模拟启动时,按照当地经验和厂家提供的参数,多次启动都未能成功。业主俄罗斯天然气工业股份公司(俄气)、总承包商NIPIGAS公司和项目当地工程师都认为,需要更换更大功率的变压器或增加电缆。
项目设计部经理薄光学回忆说,项目设计部联系西南分公司电气工程师,与业主和压缩机厂家代表沟通,核对压缩机数据,落实现场工况,提出新的参数曲线和测试方案。“比如,将电机在最小电压下的延迟时间由3秒改为5秒,但厂家就是不同意调整现场参数。业主总部派出领导和专家,专程从莫斯科飞到现场,又进行了3次测试,都获得成功,厂家这才同意调整现场参数。”
4月2日,首台压缩机机组成功完成启动测试,保证了业主要求的时间节点,也为后续压缩机组顺利投运铺平了道路。
目前,AGPP项目一至五期工程设计已基本关闭,累计提交设计文件10.7168万份,约为国内同类项目的5倍。西南分公司AGPP项目经理彭磊说:“与福陆合作,让我们对如何按照国际模式进行设计表达等有了更深的理解。我们的天然气处理和增压技术水平正在接近国际一流设计公司。”
项目质量控制人员正在进行管线焊接外观质量检测。
挑战大件运输
AGPP项目共有各类物资约25万吨,其中包含75台超大件设备运输。项目所在的阿穆尔州自由城基础设施老旧,50吨以上设备进入俄罗斯境内后,只能通过河运方式运抵现场。
业主将超大件设备运输风险设为最高级,要求全部通过海运进入俄罗斯,再通过驳船河运至项目现场码头,由专业公司MAMMOET完成“最后一公里”运输。按照该方案,仅一期工程25台超大件设备就需要配载5条驳船,运输成本将严重超出预算。
CPECC采购中心运输组与项目采购部派出专人,实地走访黑河、满洲里和布拉戈维申斯克口岸,落实通关细节,并远赴哈巴罗夫斯克、莫斯科,调研船运公司驳船运输能力并开展商务谈判,尽最大努力争取驳船资源及“最后一公里”的运费降价空间。
“驳船运输在公司海外项目大件设备运输史上的案例非常少,当地具备运输能力的资源又有限,跑了3家公司才落实。”项目采购部物流经理邹文说。
经过多次调研和测算,CPECC最终提出了海河联运、陆河联运互为补充的方案,即100吨以上设备走海运到俄罗斯德卡斯特里港,100吨以下设备从公路运输至中国黑河口岸,再换装驳船运至现场。项目采购部经理赵毅说:“起初,业主对我们的方案不放心,每个环节都盯得非常紧。”
光锁定驳船还远不够,保证这些长周期设备按期交货也至关重要。只有这样,才能赶在6月至9月适航期完成装船发运。
经过各方的共同努力,2019年6月3日,一期工程6台超大件设备经黑河口岸出关,换装驳船后,经结雅河(阿穆尔河支流)运抵现场码头,全程近3000公里;6月14日,15台超大件设备从天津港直航德卡斯特里港,换装驳船后,从阿穆尔河顺流而下;7月20日,设备抵达现场码头,全程约6000公里。
第一批超大件设备安全、准时运到现场,让赵毅他们松了一口气,也为他们赢得了业主的信任和尊重。“整个项目75台超大件设备一共发运了3批,与原方案相比,总运输成本下降30%左右。”赵毅说。
项目管理人员(右)和分包商员工沟通施工技术问题。
攻克极寒施工
疫情让全球大部分项目建设按下“暂停键”,但在AGPP项目,来自YAMATA公司、CPECC第七建设公司的8000多名建设者,在做好防疫的前提下坚守在施工现场。
面对施工现场长达7个多月、最低气温零下40多摄氏度的极寒天气,项目总经理宋跃军用自己的亲身感受告诉记者:“工作两小时必须到有暖气的休息室待一会儿,否则会被冻伤。”
项目施工部经理郭超记得,2018年12月底,为保证第一列装置首台压缩机基础混凝土浇筑一次完工,他组织人员清除施工区域20厘米厚的积雪,为压缩机盖了一个长20米、宽5米、高3米的“暖棚”,用8台热风炮连续烘了一周,才完成了压缩机混凝土浇筑和养护工作。
过了施工关,还有试压关。一期工程管道总长度157公里,多达2800个试压包。早在去年年初,项目总经理助理、试压协调组组长叶永光就开始谋划并提出方案,指导YAMATA公司圆满完成试压任务。
今年4月30日,第一列原料气脱水脱汞装置生产出合格干气,输送到P1标段的天然气脱液态烃和氮氦提纯装置;5月25日,从P1标段干气中分离出的纯净天然气,通过天然气压缩系统增压后,源源不断向中俄东线输送,标志着AGPP项目第一列生产线顺利投产;6月9日,项目第一列生产线投产庆典仪式在自由城举行。
第一列生产线的成功投产,让宋跃军这位坚守项目20个月的中国石油“老兵”,终于可以放心回国休息一下,好好陪陪家人了。接下来,还有更艰巨的任务等着他和大家去完成。
AGPP项目一期工程全景。师喜军 供图