中国石油:强化装备完整性管理 提升本质安全水平
进入新发展阶段,集团公司提出了建设基业长青的世界一流企业目标,这为装备的科学化管理提出了更高要求。随着集团公司产业链不断延伸,装备的复杂性、专业化程度、信息化水平越来越高,对装备管理的要求和期望不断增加。集团公司明确要求,要借鉴先进企业装备完整性管理经验,抓好集团公司装备完整性管理工作。
开展装备完整性管理是贯彻落实集团公司治理体系和治理能力现代化的重要举措,是推进装备管理工作高质量发展的重要抓手。工程和物装管理部借鉴国内同行的先进管理经验,认真研究将装备完整性管理确定为集团公司“十四五”装备管理的重要方向和有力抓手,围绕装备可靠性提升发力,结合专业特点和管理现状,按照试点探索、有序推进、成熟推广的步骤组织开展。2020年以塔里木油田、长庆石化、广西销售和川庆钻探为试点单位,开展集团公司装备完整性管理试点工作,以点带面努力构建中国石油特色的装备完整性管理模式。
塔里木油田突出风险管控 加载智慧“芯片”
记者 张思敏 通讯员 柳楠
中国石油网消息 在装备完整性管理上动脑筋,优化压缩机运行工况。截至6月20日,塔里木油田东河油气开发部通过优化设备运行等措施,累计节能4500吨标煤。
塔里木油田始终站在保障国家能源安全的政治高度,不断对标提升管理水平,面对装备完整性管理的“全国卷”,精心烹制“私房菜”,向突出风险管控“精准落子”、与智能化发展有序“接轨”,全力将试点打造为示范。
3月底,塔里木油田编制的《油气田地面工艺设施用电加热器》企业标准入列集团公司重点实施标准目录。此标准旨在实现相关设备全生命周期风险可控,填补行业标准空白。
把技术成果转化为管理标准,是塔里木油田精益求精推进装备完整性管理的一个缩影。在持续建立特色的装备完整性管理模式的进程中,塔里木油田多年来形成特种设备全生命周期“六严”管理模式,共消除隐患1.3万余项;形成防爆电气“六优”管理模式,共削减设备问题6.1万台(次)。
今年,塔里木油田坚持“继承与发展、分阶段分步骤、先试点后推广”,以全生命周期分类综合施策管控风险为抓手,推动装备完整性管理,落实7方面举措,实现装备本质安全、性能优良、绿色高效。
精益求精,是塔里木油田提升装备管理水平的态度,更是以安全绿色护航“稳增长”的责任。1至5月,该油田井控装备故障率同比降低36.7%,钻井事故复杂时效同比降低2.82%,创近5年最好水平;落实注气压缩机全生命周期科学管理提高注气效率,保障天然气调峰和战略储备需求。
截至6月23日,塔里木油田迪那油气开发部迪那处理站为各类设备建立“档案”,完成14项清单、75个台账。“清单+台账”巡检模式下,该站全员常态化隐患排查工作气象一新:每日排查发现隐患数量上升35%,较大隐患占比上升40%。风险管控更有效,设备本质安全更靠实。
塔里木油田践行“三好三优”管理策略——前期“选好”装备、强化“优生”管理,中期“用好”装备、实现“优育”管理,后期“管好”装备、实现“优化”管理,促进管理提升由点及面、推己及人。
以装备管理示范区为“X轴”,以典型管理经验为“Y轴”,塔里木油田建立装备完整性管理立体“坐标”,目前已建成牙哈处理站往复式压缩机示范基地,压缩机单机运行超12万小时,综合完好率98.5%以上,获评“高压循环注气全球模范现场”。
“智能工厂切实推动安全管理实现关口前移,提升工作效率。”6月24日,塔里木能源公司设备技术部副主任程会武说。该公司通过打造信息化工业化深度融合的智能工厂,实现关键生产设备全生命周期、生产工艺全流程数字化管理。
装备完整性管理与数字化转型智能化发展“接轨”,逐渐成为塔里木油田发展中的智慧“生态”。今年,在建成设备和物资管理两个信息化平台的基础上,塔里木油田从装备、管理、经营决策入手,推动设备精益化管理、智能化发展,逐步建立具有全面感知、自动操控、智能预测等功能的智能化生产运营模式,构建支撑“世界一流”的装备管理保障体系。
同时,塔里木油田持续推进在线监测智能诊断技术在关键机组的应用,加快先进技术应用和“球形储罐在线状态监测与风险评价系统研究”等科研攻关,为解决装备管理“卡脖子”问题探索更多更优解。
点评
上游企业装备设备一般使用年限较长,技术状态下滑程度较严重,具有一定安全风险。对此,集团公司启动试点工作,探索具有上游业务特点的管理方法及路径,逐步建立管理模式和体系,以达到“控制风险、提升效能”两个核心目标,保障上游生产链畅通、生产状态安全平稳。塔里木油田在存在上述装备管理工作特点的同时,有数字化建设成果的良好基础,具备基于风险管控的监测评价水平。下一步,勘探与生产分公司将坚持安全为前提,按前、中、后期三个阶段,推动标准化选型、可靠性维修和预知性维修以及设备再利用等具体措施有效落地,及时从中总结经验,在不断改进提升的基础上,充分发挥以点带面的试点推广作用。——勘探与生产分公司设备管道与海工处副处长 张晓东
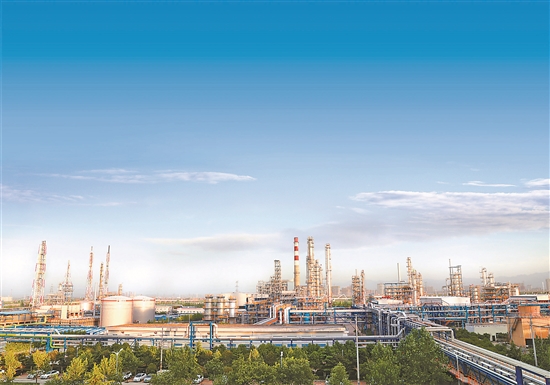
长庆石化让管理更加精细 让设备“长治久安”
记者 陈青 特约记者 朱虹
中国石油网消息 最新统计数据显示,今年前6个月,长庆石化动设备故障检修率仅为6.5%,机封、轴承等主要备件的消耗量同比再降一成。集团公司装备完整性管理试点工作在长庆石化初见成效。
炼化企业高温高压、设备数量及品种繁多,24小时不间断运行,设备既是生产的基础,也是安全的保障。
作为国家智能制造试点示范工厂,近年来,长庆石化依托工业互联网,建立了机电仪智能化平台,开展了设备健康管理,开发了智能设备管理、智能电网电气、智能仪表管理、自动平稳率监控、工控网络安全等系统,实现了设备在线巡检、故障预报警、高温在线测厚、数据统计、预知性维修等智能化应用,并通过三维数字化平台向生产、设备、安环、资产等业务领域提供可视化空间和动静态数据集成服务。
“装置智能水平的提升,使我们拥有了大量‘动、静、电、仪’设备的运行数据,在探索如何利用这些数据使设备管理更科学,检维修更合理、更经济的过程中,国际通用的‘设备完整性管理体系’,成为我们研究的重点课题。” 长庆石化公司总经理助理赵飞介绍说,炼化企业通常以完好率、故障率等指标来评价设备运行状况,而设备完整性管理体系采用的装置可靠性指数、维修费用指数等,可实现全球对标。
2021年3月,长庆石化成为集团公司4家装备完整性管理试点单位之一。按照试点方案,长庆石化将从设备风险分级、检维修策略制定、故障管理、完善KPI、大检修全生命周期管理等方面开展工作;这要求设备管理及技术人员充分理解企业运营安全、非计划停机时间等KPI指标,并掌握FMEA、RCM等完整性分析技术方法的应用。为此,长庆石化首先在新理念落地生根上下功夫。
“刚开始参加培训,很多内容听不懂,感觉无从下手。”一位项目成员回忆道。经过向集团公司试点支持机构、资深专家和国内先进企业请教,长庆石化设备管理团队深刻认识到,设备完整性管理并非抛弃原有的管理理念和模式,而是通过融入新的理念和技术方法,来保证设备运行状态的完好性。
“完整性管理体系的构建是一项系统工程,需要全员参与。我们的探索紧密结合自身智能化发展,从对生产运行影响较大的设备入手,逐步向其他设备推广,最终建成长庆石化完整性管理体系,并为炼化板块提供可借鉴模板。”长庆石化设备管理处处长索涛说。
在炼化板块的指导和安全环保院的帮助下,长庆石化目前已顺利完成第一阶段试点任务。安装使用了设备可靠性管理专业软件,完成了1740台设备的层级分解工作,开展了关键设备RCM分析、仪表设备FEMA分析,按照公司级、专业级、运行部级、装置级梳理了KPI指标,上线了智能检修平台,开展了人员能力建设培训,编写了公司装备完整性管理工作手册,梳理并优化了组织架构。
“设备完整性管理很有意义,现在预知性检修比率已达到55%,设备故障大幅减少。”运行四部设备组组长闫华负责的连续重整装置氢增压机,已连续运行了18个月。
应急操作和抢修作业的大幅降低,是设备专业管理对安全平稳生产的最大贡献。“可靠性分析和风险管控已成为我们的工作常态。”长庆石化运行一部设备技术员刘刚认为,深化完整性理念,应用完整性工具,提高了主动维修的积极性,使预防性维护和预知性维修更精准、高效。目前,长庆石化设备完好率保持在99.9%以上。
点评
设备完整性管理是当前国内外企业设备管理的先进理念和主流趋势。长庆石化作为中国石油炼化企业设备完整性管理试点单位,大胆探索,勇于实践,在设备管理方面进行了一系列机构优化和流程再造,将完整性管理理念融入到日常设备管理中,为完整性管理理念的推广应用树立了榜样。下一步,将通过技术措施与规范管理相结合,不断强化系统管理和风险管理理念,推动炼化设备管理从传统的经验化、碎片化管理方式,向标准化、智能化、一体化的体系思维管理方式转变,逐步建立一套具有国际先进水平和中国石油特色的炼化设备完整性管理体系。——炼油与化工分公司装备管理处处长 赵斌
广西销售强化设备“智”理 彰显五大成效
记者 王剑英 通讯员 刘祥
中国石油网消息 6月26日早上7点半,广西销售鲁班加油站交接班期间,加油员宋海强在加油现场开展当天的设备巡检。他在手机上登陆设备智管APP后,一边扫描粘贴在设备区域的NFC标签,一边将巡检信息录入平台。整个巡检过程靠一台手机搞定。
“以前每天巡检要做巡检手工台账,巡检问题要登记到不符合项整改台账,问题报修又要另行申请,不仅流程烦琐,还费时。如今,加油站设备巡检的全过程闭环管理依靠设备一体化智能管控平台都能实现,不仅员工解放双手、节约时间,还避免了检查漏项,加油站更安全。”鲁班站经理林飞高兴地告诉记者,自从去年10月加油站上线设备智管平台后,员工告别手工台账,将更多的时间和精力放在加油站提质增效上。截至6月28日,该站主油、非油完成率均超过进度计划。
这是广西销售开展装备完整性管理体系试点的一个缩影。据广西销售相关负责人介绍,广西销售自主探索建立设备管理信息系统,始于2015年。由于较好的装备管理数字化基础,2021年被销售公司列为设备完整性管理及一体化管控平台项目的试点单位之一。受疫情等影响,为确保试点工作有序推进,广西销售迅速成立以主要领导为组长的试点工作小组,采取“线上视频培训+远程指导+个别现场指导”相结合的形式,展开需求调查分析、平台功能设计、平台功能开发、设备分类分级、系统数据初始化、系统功能测试等工作,先后召开22次推进会,按照日跟进、周通报原则对标对表推进项目落地,广西近600座加油站和8座油库的2万余台设备上线设备一体化智能管控平台。今年以来,板块智能管控平台中的检维修管理、完好性检查、预防性管理三项指标排名销售公司榜首,取得较好管理预期,圆满完成销售公司交办的平台试点任务。
与此同时,在销售公司的科学指导下,广西销售创新思路,以问题为导向,以实践丰富理论,于今年年初开展装备完整性管理体系试点建设工作,针对性地进行体系架构总体策划,逐步完成各层级文件编制工作,形成“管理手册+程序文件+作业文件”三级体系架构,装备制度体系文件编制成型。
特别值得一提的是,设备一体化管控平台的上线,不仅使广西销售装备管理质量得到有效提高,更彰显出五方面管理成效。其一,实现对设备全生命周期数据的集中管理。从设备采购验收建档开始,平台就对设备的使用、检查、维保、检测、维修、改造直至报废的各过程进行监控管理,以此实现设备寿命周期费用最经济、设备综合产能最高的理想目标。其二,实现与资产平台的数据集成共享。设备一体化管控平台与集团公司资产管理平台融合集成,实现系统间数据同步共享,达到价值管理与实物管理同步调,管理统一、账实相符。其三,实现设备巡检及问题整改全闭环管理。设备巡检的问题发现、问题确认、问题解决,在平台均可实现全流程管理,有效提高设备巡检的真实性以及问题整改的及时率。其四,实现设备检维修的全过程管理。平台可实现检维修项目的计划编制、立项申请、审批、项目计划下达、施工过程管理、作业许可办理、维修验收等全过程管理,动态监管检维修的全过程,为优化检维修管理提供数据支撑。其五,实现设备保养检测的动态跟踪提醒。平台可建立各专业设备的保养检测标准,设定业务执行规则及周期,通过APP可实时推送提醒消息,督促库站做好设备预防性维护工作,降低设备故障率。
点评
在销售企业全面推行装备完整性管理,有利于深化企业对标对表管理,有利于提升设备资产价值的创造能力,有利于推进数字化转型,为销售业务的高效运行保驾护航。下一步,我们将按照集团公司工程和物装管理部的总体部署,持续做好完整性管理、一体化管控平台的融合建设,功能迭代升级,逐步实现与零售3.0、财务共享、QHSE、ERP等在用系统的集成,实现设备管理“五化”“五融合”,实现销售业务的互联互通、信息协同和数字化转型。同时,结合集团及销售公司QHSE体系审核,持续开展设备完整性管理的运行评估,提升设备完整性管理的运行水平。——销售公司工程建设处处长 王全占
川庆钻探突出装备价值创造 满足安全高效生产
通讯员 谭沁汶
中国石油网消息 截至6月底,川庆钻探上半年设备综合完好率98.15%。该公司自成为集团公司装备完整性试点企业以来,按照集团公司“适宜适用、力求实效”工作要求,基于业务主线,围绕“安全第一、科学规范、两化融合、节能环保”工作原则,以管理完整性、技术完整性、经济完整性为抓手,探索突出装备价值创造能力、满足油气安全高效生产的装备完整性管理模式和路径,并在具有专业特点的二级单位开展试点试行,为安全完好、经济高效、平稳运行的装备管理目标提供了有效支撑。
4月启动以来,以装备全生命周期管理为主线,按照各周期要素管理要求,川庆钻探充分收集设备相关技术标准213项、相关规章制度文件906份,梳理ISO、行业、企业相关管理标准51项,编制装备完整性管理标准矩阵、装备完整性管理程序文件目录,形成川庆公司和川西钻探两级《装备完整性管理手册》初稿。
通过建立科学、合规、全面、适用的川庆特点装备完整性管理文件,推动装备全生命周期完整性管理适宜、规范、高效,实现主要专业设备综合完好率≥96%、故障停机率≤2%、设备维修费用率在3%到8%之间的目标。
依托川庆钻探自己打造的一体化信息系统(EISS),搭建了装备完整性管理信息平台。目前已实现国内215支钻井队伍系统上线运行,设备数据无纸化填报,以及6部钻机的远程实时监控,井下、试修101支基层队也已推广应用。同时以信息平台为基础,开展关键设备预警分析和系统数据应用,深挖数据利用价值,实现公司、二级单位、基层单位三个层级的装备完整性各环节全要素信息化管理。
平台通过对装备静态台账管理、动态运行数据采集、生产及工程数据融合共享、周期要素管理流程线上处理、装备经济性指标分析评价等功能,为公司装备完整性管理考核、决策提供支撑和依据。
结合多专业实际,首先在钻井专业开展装备完整性管理试点,拟建设5支数字化钻井队,以设备设施运行管理数字化为驱动,建设装备配置布置符合标准、装备完整性技术文件齐全规范、人员作业技能强、知识水平高的示范基层队。该公司以下属川西钻探钻井队伍为试点。截至6月底,川庆90027、70227队已完成了数字化营房配置和数字化井场建设,实现设备设施运行状态实时监控,设备主要部件、易损件工作时间自动记录和预警;接下来,将着力完善数字化井场装备的配置布置标准、技术管理规范等工作。
上半年,川庆公司“电代油”用电量突破2.5亿千瓦时,钻机“电代油”203井次,减少碳排放5.9万吨,减少氮氧化物排放766.7吨;推进17套载人物电动绞车、44套机械密封冲管、8套BOP移运装置等自动化机具应用;以国产替代进口、按油品质量更换润滑油的“按质换油”工作取得实效,节约710万元。
该公司按照装备配置管理标准化、运行管理数字化、技术管理规范化的现场装备完整性试点要求,着力打造钻井专业装备完整性管理示范现场,尤其是突出自动化装备配套应用、“电代油”能源管理技术规范,形成钻井现场数字化、标准化、规范化管理模板,实现“电代油”技术规范执行率100%,自动化建设完成率100%,发电机专用油消耗下降10%等。
点评
川庆钻探的装备管理特色鲜明,装备规模、技术能力和管理水平均处于中油技服的前列。在管理实践中,川庆钻探总结探索出系列经验:一是坚持标准化管理,选型配置标准化程度高,规章制度体系科学完整,装备现场模板规范构建。二是推进数字化赋能,信息技术、数字技术在装备全生命周期广泛应用,装备与工程、工艺、现场深度融合,数据价值得到充分挖掘。三是锚定安全、绿色、智能发展方向,先进装备大量投入,自动化程度显著提升,节能减排装备规模推广,尖兵重器率先应用,本质安全水平显著提升。这些宝贵经验的获得和淬炼,将为中油技服各成员企业装备的高质量发展提供有力借鉴。——工程技术分公司生产管理部副主任 杨晖